Overview of GTMI Research
Georgia Tech (GT) has a large community of talented, passionate researchers and professionals in the broad area of advanced manufacturing. At GT, manufacturing transcends the traditional notion of fabrication or machining; rather manufacturing spans the entire value-creation process of physical artifacts and related services – a convergency of manufacturing and service. Indeed, Big M Manufacturing, built under an Industry 4.0 framework, encompasses all innovative endeavors associated with design, analysis, prototyping, testing, production, distribution and supply chains and re-use of mechanical, electrical & electronic, chemical, and biological products.
The diagram below denotes major areas of research in Big M Manufacturing at GT, from additive manufacturing and biomanufacturing to supply chains and sustainable design & manufacturing. A number of unique characteristics separate GT manufacturing R&D from most other academic research groups:
- Georgia Tech Manufacturing Institute (GTMI) always approaches manufacturing from a systems perspective. All engineered systems today and in the future are complex systems of systems. A slight change in one component will affect the responses and behaviors of other components and hence the overall performance of the system. This is true from additive to composites to hypersonics. On-going campus-wide signature initiatives such as additive manufacturing as a system, and hypersonics as a system are good examples.
- Advanced manufacturing, innovative materials and data analytics are the three common threads in most GT manufacturing R&D projects. Digital thread and digital twins, cyber-physical systems, and digital transformation are essential pillars. Regarding the digital aspect of Big M Manufacturing, GTMI researchers have deep expertise in data security and monetization. Secure manufacturing and supply chains is an on-going effort that involves faculty and students from several schools at GT.
- GT is a globally recognized leader in basic research. Moreover, GTMI is a major proponent and thought leader in translational R&D and concurrent deployment of technology readiness, manufacturing readiness, business case readiness and ecosystem readiness, i.e., fully integrated technology readiness (TRL) / manufacturing readiness (MRL) / business readiness (BcRL) / ecosystem readiness (EcRL). (Engineering and manufacturing: concurrent matruation of xRL - PDF). Translational R&D addresses xRL 4-7 challenges including but not limited to production scale-up or scale-out.
- TRL / MRL 4-7 projects are carried out in the 20,000 sq. ft. Advanced Manufacturing Pilot Faculty, or AMPF, where GT researchers and students work with industry and government partners on translational R&D. It is a well-known “teaching factory.”
- Education and workforce development (EWD) is an integral part of what we do. GTMI manages an advanced manufacturing certificate program and participates in numerous EWD programs with the specific purpose of creating a large talent pool in advanced manufacturing.
- Infrastructure development is another GTMI pillar. Internally within GT, GTMI supports several basic and translational R&D facilities and maintains the best possible environments for GT faculty, staff, and students. Externally GTMI represents GT in key national initiatives and partnerships such as Manufacturing USA Manufacturing Innovation Institutes, formerly known as the National Network of Manufacturing Innovation.
- GT faculty are leaders and active participants in manufacturing policy discussion and standards development. GT faculty are strong advocates for advanced manufacturing. For example, G.P. Bud Peterson, former GT president, was appointed to the Advanced Manufacturing Partnership Steering Committee, under the auspices of the President’s Council of Advisors on Science and Technology. Several high-profile manufacturing initiatives, including the Manufacturing USA network of Manufacturing Innovation Institutes came as the result of the AMP Steering Committee’s recommendations.
- GTMI fully believes in strategic partnerships with companies of all sizes and government at all levels. GTMI grows and excels with our strategic partners symbiotically.
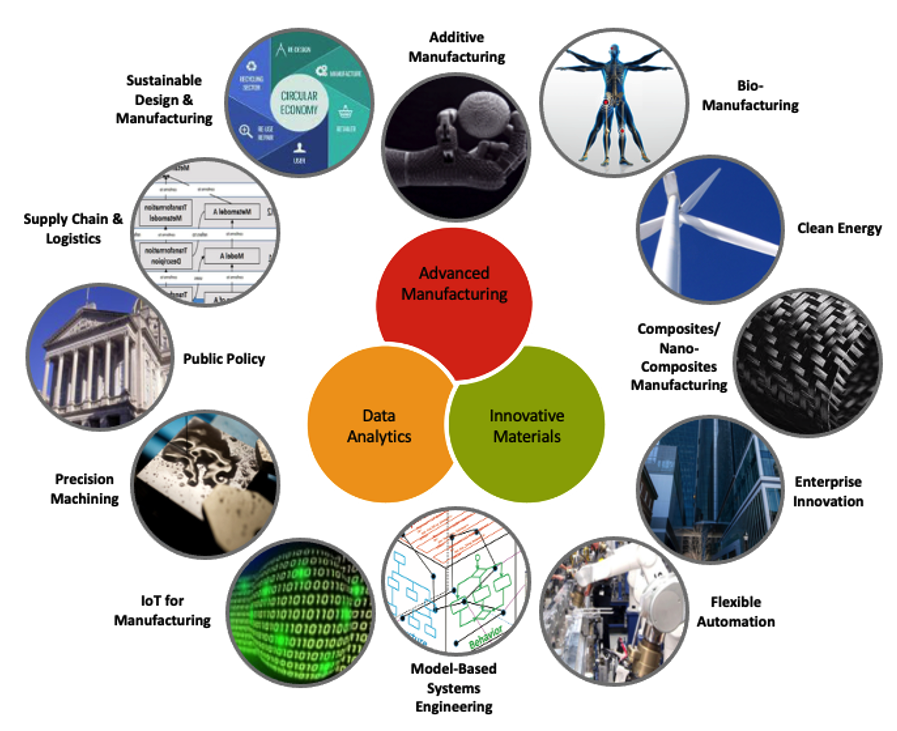
A Glimpse Into Smart Manufacturing
Smart manufacturing is about harnessing new technologies to enable faster, better, cheaper. Several new technologies help to achieve those goals. GTMI is helping to take the manufacturing community to new heights and ensure competitive advantages.
Awards, Recognitions, and Impact
• Awarded a $65 million grant from the U.S. Department of Commerce’s Economic Development Administration (EDA) to support a statewide initiative that combines artificial intelligence and manufacturing innovations with transformational workforce and outreach programs
• Named a Boeing Supplier of the year and one of the company’s eight university partners
• Awarded a grant to develop and lead the Consortium for Accelerated Innovation and Insertion of Advanced Composites (CAIIAC)
• Named a Caterpillar University Center of Excellence in Machine-Related Research
• A Siemens research partner for 25 years and counting
• Developer of international standards that facilitate collaboration and data exchange within numerous manufacturing industries, including additive manufacturing, IoT for manufacturing, and composite fabrication and inspection
• Assisted in the development of 20 spinoff companies
• Together with other GT academic and research units, GTMI has served nearly 2,800 companies, contributed to $408 million in increased sales, $64 million in operating costs saved and 2,507 jobs created/saved
Facilities for Basic and Applied Research
GTMI has invested over $58 million in its manufacturing research complex, comprising 400,000 square feet of state-of-the-art R&D facilities, including the GTMI headquarters at the Fuller E. Callaway Jr. Manufacturing Research Center building, the J. Erskine Love Jr. Manufacturing Building and the Manufacturing Related Disciplines Complex; the Applied Manufacturing Pilot Facility (AMPF) on campus at the intersection of 14th Street and Hemphill Avenue, where researchers and students work alongside industry partners on industry-sponsored translational projects; and a network of labs across campus.